Plastic extrusion for creating standardized, premium parts
Key Advantages and Factors To Consider of Implementing Plastic Extrusion in Your Jobs

Understanding the Fundamentals of Plastic Extrusion
Plastic extrusion, a staple in the production sector, is a process that entails melting raw plastic product and reshaping it right into a constant account. This profile, as soon as cooled, can be cut into wanted sizes or curled for later use. The charm of plastic extrusion depends on its flexibility. A wide variety of items, from piping to window frames, can be generated. The procedure needs an extruder, an elaborate machine with a warmed barrel, a turning screw, and a die at the end. The plastic material, in the kind of pellets, is fed into the extruder, where it's thawed and required through the die, taking its form. The option of plastic and the design of the die establish the product's characteristics.
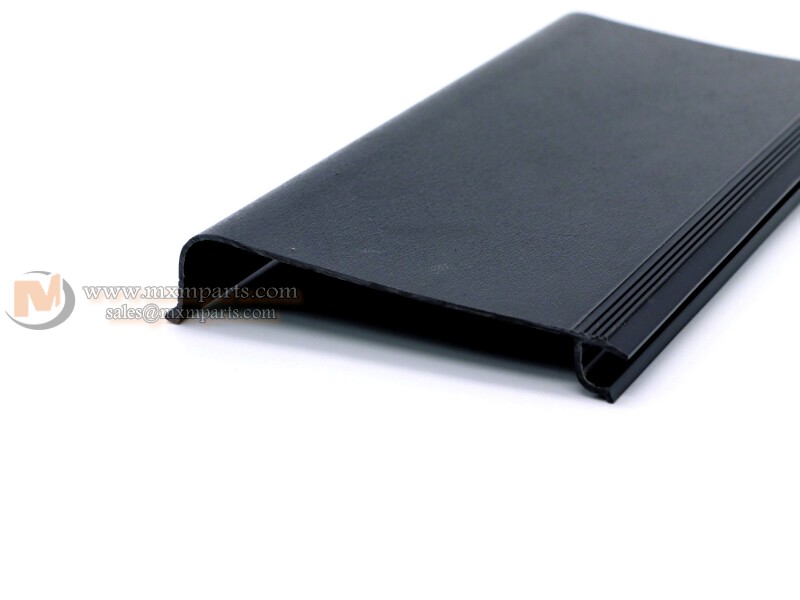
The Economic Advantage of Plastic Extrusion
The economic benefit of plastic extrusion lies mainly in two areas: cost-efficient material production and valuable production rates. With plastic extrusion, businesses can generate high volumes of product at a reduced cost compared to various other approaches. The process flaunts a remarkable manufacturing speed, considerably minimizing time and more boosting its financial viability.
Affordable Material Production
A considerable advantage of plastic extrusion is its impressive cost-effectiveness. This manufacturing procedure permits continuous, high-volume production with minimal waste, which translates into lower costs. The raw materials used, usually plastic pellets, are fairly low-cost contrasted to various other compounds (plastic extrusion). The procedure itself needs less energy than lots of various other manufacturing techniques, additionally decreasing expenses. In addition, the extrusion procedure allows for a high level of precision in shaping the plastic, decreasing the requirement for pricey post-production modifications or improvements. Moreover, the toughness and longevity of extruded plastic items commonly mean much less require for substitutes, adding to lasting cost savings. All these aspects make plastic extrusion an extremely cost-effective option for lots of projects, supplying an appealing balance between cost and efficiency.
Beneficial Production Speeds
While maintaining the cost-effectiveness of the materials, an additional noteworthy benefit of plastic extrusion lies in its fast manufacturing rates. This performance in the production process is connected to the continual nature of the extrusion procedure, enabling high-volume manufacturing in a fairly brief time span. The speed of manufacturing straight associates to a decrease in labor costs and an increase in output, thereby improving the overall financial practicality of the process. In addition, the fast-paced manufacturing does not endanger the top quality of the final item, guaranteeing constant and trustworthy outcomes. This mix of high quality, rate, and cost-effectiveness highlights the considerable financial benefit of implementing plastic extrusion in different projects.
Adaptability and Personalization: The Toughness of Plastic Extrusion
One of the prominent toughness of plastic extrusion depends on its adaptability and modification capacity. These qualities unlock to unlimited layout possibilities, giving producers the capacity to tailor products to details requirements. This heightened degree of personalization not just improves product performance but also considerably boosts item individuality.
Limitless Style Opportunities
Plastic extrusion radiates in its ability to supply almost endless design opportunities. This approach supplies freedom to produce intricate forms and intricate profiles, a feat difficult to accomplish with various other construction techniques. Owing to the fluid nature of liquified plastic, the procedure is versatile enough to generate a varied variety of types, sizes, and measurements. The plastic can be manipulated to match distinct requirements, permitting the production of tailored geometries and meeting details customer needs. Plastic extrusion can take care of a selection of plastic types, increasing its application extent. This adaptable technique, as a result, offers a vast variety of sectors from building and construction to auto, packaging to electronics, and beyond. With plastic extrusion, the style opportunities are essentially endless.
Increasing Product Individuality
The versatility of page plastic extrusion try this can significantly enhance product individuality. This process permits designers to explore various shapes, sizes, and colors, giving them the freedom to develop distinct products that stand out in the marketplace. It is this customization that provides a distinct identification per product, distinguishing it from its competitors.
In enhancement to its aesthetic advantages, the customizability of plastic extrusion additionally offers functional benefits. Designers can modify the buildings of the plastic according to the specific demands of the application, boosting the product's functionality. They can make the plastic a lot more adaptable, more long lasting, or a lot more resistant to heat, depending on what the product needs. Therefore, plastic extrusion not just increases item originality however likewise its utility and bankability.
Design Limitations in Plastic Extrusion: What You Need to Know
Just how can make restrictions possibly influence the process of plastic extrusion? While plastic extrusion is versatile, style limitations can stop its advantages. Specific facility designs might not be viable as a result of the limitations of the extrusion procedure, potentially limiting the creation of detailed accounts. The process is much less suitable for multi-chambered or hollow structures. In addition, the extrusion process might not constantly give the preferred surface coating, particularly for those requiring high gloss or optical quality. Product choice can also posture challenges, as not all polymers appropriate for extrusion. High-temperature Visit Your URL resistant plastics, for example, may provide problems. Understanding these constraints is essential for efficient execution of plastic extrusion in your jobs. plastic extrusion.
Examining the Ecological Influence of Plastic Extrusion
While recognizing style restrictions is a considerable aspect of plastic extrusion, it is equally important to consider its environmental ramifications. The process of plastic extrusion entails melting plastic materials, possibly launching unsafe gases into the setting. Further, the resulting items are often non-biodegradable, adding to land fill waste. However, innovations in innovation have permitted even more environmentally-friendly methods. As an example, making use of recycled plastic products in the extrusion process can minimize environmental impact. Additionally, creating biodegradable plastic choices can assist reduce waste problems. Examining these ecological factors is essential when implementing plastic extrusion projects, making sure a balance between performance, cost-effectiveness, and environmental duty.

Study: Effective Projects Making Use Of Plastic Extrusion
Success tales in the area of plastic extrusion are plentiful, showing both the versatility and efficiency of this manufacturing process. plastic extrusion. Another effective case is the manufacturing of plastic movie for packaging and agriculture. These instances illustrate plastic extrusion's crucial duty in different markets, proving to its flexibility, cost-effectiveness, and reputable result.
Conclusion
In verdict, plastic extrusion offers a affordable and effective technique for producing complicated shapes with very little waste. Including plastic extrusion into projects can lead to successful outcomes, as evidenced by many situation researches.
Plastic extrusion, a staple in the production market, is a process that involves melting raw plastic material and reshaping it right into a continuous profile. Plastic extrusion can take care of a range of plastic types, broadening its application extent.Exactly how can create limitations possibly impact the process of plastic extrusion? The procedure of plastic extrusion involves melting plastic products, possibly releasing harmful gases right into the environment. Using recycled plastic products in the extrusion procedure can reduce ecological impact.